ISI Journals by Emanoil LINUL

In this paper is presented the behaviour of PUR foams under mixed mode loading. Closed cell rigid... more In this paper is presented the behaviour of PUR foams under mixed mode loading. Closed cell rigid PUR foams having three different densities 100, 145, and 300 kg/m 3 were investigated. Experiments were performed using asymmetric semi-circular bend (ASCB) and Assymmetric Four-Point Bend (AFPB) specimens. The obtained crack initiation angles established for ASCB specimens were compared with four fracture criteria MTS, SED, G max and ESIF, and a good agreement was observed. When testing AFPB specimens, and calculating the normalized stress intensity factors it is important to obtain a correct crack propagation, that is to impose proper geometrical dimensions as not to affect the initial crack tip. The eXtended Finite Element Method (XFEM) is a complementary powerful numerical tool used to analyze crack initiation and propagation only if the numerical model is correctly calibrated and all the influencing parameters are properly understood.
Mixed mode four-point testing is performed on polyurethane foams. This paper presents only the re... more Mixed mode four-point testing is performed on polyurethane foams. This paper presents only the results on the stress intensity factors (SIFs) obtained experimentally for a density of 325 kg/m 3 , although tests were done for three foam densities. An asymmetric four-point bending setup was used for determining the critical SIFs in Mode I and Mode II, and discussions on the influence of the initial crack length on the SIF values are done. As initial crack length is increased the theoretical predictions give a better comparison to experimentally obtained results.
Micromechanical models used to predict mechanical and fracture properties of brittle metallic foa... more Micromechanical models used to predict mechanical and fracture properties of brittle metallic foams are validated experimentally for closed-cell aluminium foam (AlSi12Mg0.6) prepared by powder metallurgy route. Compression, tensile, tensile on notched specimens and fracture toughness tests were carried on, and the results are presented together with micromechanical models from literature. Moreover, the Digital Image Correlation technique was applied to identify the failure mechanisms of aluminium foams. Finally, the Theory of Critical Distances was employed to predict the fracture load of notched specimens. The novelty of the study is that the inherent stresses and critical distances were obtained by employing micromechanical analysis.

The failure-mode maps of composite sandwich beams can provide useful information about the influe... more The failure-mode maps of composite sandwich beams can provide useful information about the influence of different design parameters on the failure behaviour of such components. Failure mode of sandwich beams with different cores and different faces were investigated in the experimental program. Foams with 40 and 200 kg/m 3 densities were used as core material, while Glass-Fibre Reinforced Polymer (GFRP), polyester, epoxy and aluminium are the faces materials. Three-point bending tests were carried out for sandwich beams. In order to characterize these sandwich materials first were carried out a statistical analysis of the cellular structure for two different densities of the core material above mentioned. The sandwich core morphology and cells dimensions were studied before testing through scanning electron microscopy (SEM) and pore diameter versus frequency of pores histogram were plotted. After statistical analysis were performed static compression tests. These compression tests have had as objective the determining of the main mechanical properties such as Young's modulus and yield stress values. The results obtained from the static compression tests were used for the analytical determination of failure-mode maps of sandwich beams. Finally, the failure-mode maps were constructed for five considered sandwich types and validated by the experimental results. Each failure-mode map is characteristic for a family of sandwich beam designs.
This work investigates the mechanical properties of polyurethane rigid foams by means of Dynamic ... more This work investigates the mechanical properties of polyurethane rigid foams by means of Dynamic Mechanical Analysis (DMA) tests and Impulse Excitation Technique (IET). DMA tests were performed in single cantilever with a sweep in temperature (from-50 °C to 100 °C) and frequency (from 1 Hz to 100 Hz), not determining glass-transition in the test parameter interval. IET tests were used to determine the dynamic modulus of elasticity, showing good accordance with DMA results
The notch effect in Polyurethane materials of different densities is investigated. Tensile specim... more The notch effect in Polyurethane materials of different densities is investigated. Tensile specimens with lateral V and U symmetric notches and with holes of different diameters were tested. The material parameters inherent stress and critical distance are determined using a linear elastic finite element analysis in conjunction with experimental results of average maximum load. The paper proposed an original correlation between critical distance and the cell diameter of the cellular structure, respectively between inherent stress and the ultimate tensile strength of Polyurethane materials. Then for single edge notch specimens a relationship between critical distance and applied mixed mode is found and successfully applied to assess the brittle mixed mode of Polyurethane materials.
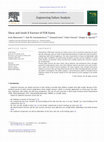
Polyurethane (PUR) foam materials are widely used as cores in sandwich composites, for packing an... more Polyurethane (PUR) foam materials are widely used as cores in sandwich composites, for packing and cushioning. They are made of interconnected networks of solid struts and cell walls incorporating voids with entrapped gas. The main characteristics of foams are lightweight, high porosity, high crushability, and good energy absorption capacity. Fracture toughness in mixed mode loading is of particular interest because foam cracking weakens the structure's capacity for carrying loads. Present paper assesses the shear elastic (shear modulus) and mechanical (shear strength) properties of polyurethane foams. Also, three different types of specimens were used to determine mode I and mode II fracture toughness. The shear modulus, shear strength and fracture toughness increases with increasing foam density. Also the effect of loading direction and loading speed is investigated. The authors propose a micromechanical model to estimate fracture toughness based on the tensile strength of the solid material and the topology of the cellular structure.
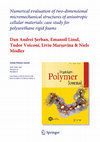
This paper deals with evaluating the elastic
response of several micromechanical structures used ... more This paper deals with evaluating the elastic
response of several micromechanical structures used for simulating cellular materials under compression. For this
study polyurethane rigid foams were investigated, having
three relative densities: 0.085, 0.124 and 0.256. Their
microstructure was analysed using SEM images, determining
four types of cells that were consequently designed
using specialized CAD software: square cells with circular,
quadratic and/or hexagonal orifices and hexagonal
cells. An interdependent variation of the cells’ geometrical
parameters of the proposed structures was determined to
obtain geometrical variations at a required relative density.
Finite element analysis simulations were performed on
the designed microstructural models using a linear elastic
material model for the cell struts, resulting in the variation
of the elastic modulus of the structure with the variation in
cell geometry parameters. The final objective of this work
was to determine anisotropic bi-dimensional micromechanical
models for the studied cellular material that provides
accurate results in compression on both loading directions.
The anisotropic models for the proposed cell structures
were obtained by generating irregular geometries which
provided extra variables for the cell geometry parameters.
It was determined that some cell geometries are suitable
for simulating lower relative density materials while other cell geometries provide good accordance with experimental
data for higher relative density materials.
Many efforts have been made in recent years to determine the fracture toughness of different type... more Many efforts have been made in recent years to determine the fracture toughness of different types of foams in static and dynamic loading conditions. Taking into account that there is no standard method for the experimental determination of the fracture toughness of plastic foams different procedures and specimens were used. This paper presents the poly-urethane foam fracture toughness results obtained for different foam densities. Two types of specimens were used for determining fracture toughness in modes I, II and a mixed one, and also the size effect, loading speed and loading direction were investigated. The paper proposed correlations for density, cell orientation and mixed mode loading based on the experimental testing results.
International Journal of Solids and Structures, Nov 2, 2012
Polymer Testing, Mar 9, 2013
Iranian Polymer Journal, Aug 17, 2011
ISI Proceedings by Emanoil LINUL

Cellular plastics are light weight structures with many applications in civil, aeronautical, auto... more Cellular plastics are light weight structures with many applications in civil, aeronautical, automotive and mechanical engineering. Properties of cellular materials depend on the properties of the solid material, on the shape and dimensions of the cellular structure and on the relative density of the cellular material. Most of cellular plastic materials are crushing in compression and have a brittle behavior in tension. The effect of notches represents an important issue in such materials, taking into account that for packing applications for example, notches/holes should be introduced in the cellular material. This paper investigates the effect of notches in compression for three different densities 100, 145 and 300 kg/m 3 polyurethane (PUR) foams. Experimental investigations were performed on rectangular blocks of 100x100x25 mm with 16, 28 and 40 mm central holes. The mechanism of damage was monitored with an IR camera FLIR A40M. Purpose of the numerical simulations was to calibrate a material model, based on compression test for un-notched specimens using the CRUSHABLE FOAM models implemented in ABAQUS SIMULIA. Then the material models were used to simulate the experimental tests on notched blocks. Good agreement was obtained for the load-displacement curves obtained experimentally and from simulation. Also the plastic deformation patterns observed experimentally by IR thermograpghy were obtained numerically using the CRUSHABLE FOAM material model.

Cellular materials represent a new class of materials; main parameters that characterize the cell... more Cellular materials represent a new class of materials; main parameters that characterize the cellular structure are relative density, shape of the cell (open or closed), wall thickness and cell diameter. The purpose of this paper is to investigate the microstructure of foams materials and also to determine the flexural properties of this rigid PUR foams using Digital Image Correlation (DIC). The rigid PUR foams cells morphology and pore distribution for three densities (100, 145 and 300 kg/m 3) were studied before testing through scanning electron microscopy. Determination of flexural properties was carried out on rectangular beam samples using ARAMIS 2D system. This method provides a substantial increase in accuracy for measuring strain and is based on the calculation of surface deformation using a set of digital images from undeformed stage to different deformed stages. The specimens were subjected to static three points bending tests with loading rate of 2 mm/min, at room temperature and loading was applied in rise direction of the foam. Experimental results show that main mechanical properties such as flexural modulus and flexural strength values increases with increasing of density.
Journal of Physics: Conference Series , 2013

Key Engineering Materials, 2014
Polyurethane (PUR) foam materials represent a class of materials widely used for impact protectio... more Polyurethane (PUR) foam materials represent a class of materials widely used for impact protection and energy absorption. This paper presents a characterization of different rigid PUR foams under compressive impact loading by means of energy absorption and efficiency diagrams. Compressive properties were investigated on cubic specimens on the foams’ rise direction at room temperature with a loading rate of 3.09 m/s for three different closed-cell foams with densities of 100 kg/m3, 160 kg/m3 and 300 kg/m3 respectively. Experimental results show that the compression modulus, yield stress and plateau stress increase with density. Most of the energy is absorbed in the plateau region because of the cell deformation associated with this phenomenon, allowing greater absorption of impact energy at nearly constant load. Authors have found that both the energy absorption and efficiency diagrams are consistent and present similar results for studied foams.
Key Engineering Materials, 2014
This paper presents an experimental characterization of three different types of closed-cell alum... more This paper presents an experimental characterization of three different types of closed-cell aluminium alloy foams (AlMg1Si0.6, AlSi12Mg0.6 and AlMg0.6Si0.3) under static compressive loading. This study was carried out on half-cylindrical specimens with skin. The influence of foam density on compressive behaviour was investigated for densities ranging from 430 kg/m3 to 935 kg/m3. The compression tests were performed at room temperature (23°C) with a constant crosshead speed of 0.5 mm/min. Strain distribution, yield stress and compressive modulus values were recorded using Digital Image Correlation. Experimental results show that the mechanical properties (Young’s Modulus, yield stress and plateau stress) increase with density.
Key Engineering Materials, 2014
Key Engineering Materials, 2014
Uploads
ISI Journals by Emanoil LINUL
response of several micromechanical structures used for simulating cellular materials under compression. For this
study polyurethane rigid foams were investigated, having
three relative densities: 0.085, 0.124 and 0.256. Their
microstructure was analysed using SEM images, determining
four types of cells that were consequently designed
using specialized CAD software: square cells with circular,
quadratic and/or hexagonal orifices and hexagonal
cells. An interdependent variation of the cells’ geometrical
parameters of the proposed structures was determined to
obtain geometrical variations at a required relative density.
Finite element analysis simulations were performed on
the designed microstructural models using a linear elastic
material model for the cell struts, resulting in the variation
of the elastic modulus of the structure with the variation in
cell geometry parameters. The final objective of this work
was to determine anisotropic bi-dimensional micromechanical
models for the studied cellular material that provides
accurate results in compression on both loading directions.
The anisotropic models for the proposed cell structures
were obtained by generating irregular geometries which
provided extra variables for the cell geometry parameters.
It was determined that some cell geometries are suitable
for simulating lower relative density materials while other cell geometries provide good accordance with experimental
data for higher relative density materials.
ISI Proceedings by Emanoil LINUL
response of several micromechanical structures used for simulating cellular materials under compression. For this
study polyurethane rigid foams were investigated, having
three relative densities: 0.085, 0.124 and 0.256. Their
microstructure was analysed using SEM images, determining
four types of cells that were consequently designed
using specialized CAD software: square cells with circular,
quadratic and/or hexagonal orifices and hexagonal
cells. An interdependent variation of the cells’ geometrical
parameters of the proposed structures was determined to
obtain geometrical variations at a required relative density.
Finite element analysis simulations were performed on
the designed microstructural models using a linear elastic
material model for the cell struts, resulting in the variation
of the elastic modulus of the structure with the variation in
cell geometry parameters. The final objective of this work
was to determine anisotropic bi-dimensional micromechanical
models for the studied cellular material that provides
accurate results in compression on both loading directions.
The anisotropic models for the proposed cell structures
were obtained by generating irregular geometries which
provided extra variables for the cell geometry parameters.
It was determined that some cell geometries are suitable
for simulating lower relative density materials while other cell geometries provide good accordance with experimental
data for higher relative density materials.
Linear Elastic Fracture Mechanics. Fracture toughness in mixed mode loading is of particular interest because foam cracking
weakens the structure's capacity for carrying loads. Four fracture criteria (Maximum circumferential tensile stress, Minimum strain energy density, Maximum energy release rate, Equivalent stress intensity factor) were considered for evaluation of mixed mode fracture of three closed cell rigid polyurethane foams with densities: 100, 145 and 300 kg/m3. Mixed mode fracture tests were performed using asymmetric semi-circular specimen. The equivalent stress intensity factor criterion looks to give the better prediction of mixed mode fracture. Also the effect of cell orientation and the crack propagation angle were investigated.
standard method for the experimental determination of the fracture toughness of plastic foams, different procedures and specimens were used. This paper presents the polyurethane foam fracture toughness results obtained experimentally for three foam densities. Asymmetric four-point bending specimens were used for determining fracture toughness in mode I and in a mixed one, and also the influence of the loading speed and geometry of the specimen were investigated.