転がり軸受
![]() |

転がり軸受(ころがりじくうけ)は、転動体(玉やころ)を2つの部品の間に置くことで荷重を支持する軸受。部品同士の相対的動きにより、転動体は非常に小さな転がり抵抗で自転し、同時に若干すべるような動きをする。
原始的かつ有名な転がり軸受としては、大きな岩と地面の間に丸太を何本もかませたものがある。岩を牽くと丸太が若干すべりながら回転する。後ろから丸太がはみ出したら、それを前方に移して再び岩と地面の間にかませる。これは、テーブルの上にペンや鉛筆を並べ、その上に物を置くことで再現できる。軸受の歴史については軸受を参照のこと。
転がり軸受は、軸と軌道輪(レース)の間に転動体(ローラー)と呼ばれる円柱などを置いてその隙間を埋めたものである。軸が回転すると転動体は上述の例の丸太のような動きをする。ただし、軸受は丸いので、転動体が軌道輪から外れて出ることはない。
転がり軸受は、コスト、大きさ、重さ、荷重許容量、耐久性、精度、摩擦などのトレードオフを考慮して設計される。他の軸受はこれらの特性の一部に優れているが、他の特性が転がり軸受に劣っていることが多い。ただし流体軸受は、荷重許容量、耐久性、精度、摩擦、回転数に優れ、コストの面でも転がり軸受に勝る場合がある。他にすべり軸受も転がり軸受と同程度に広く使われている。
設計
[編集]典型的な転がり軸受の大きさは直径数mmから数mで、荷重許容量は数十グラムから数千トンである。
最も一般的な転がり軸受は、玉軸受である。玉軸受は玉を転動体とし、それを内と外の軌道輪で挟んでいる。軌道輪は玉を保持する溝のついた輪である。溝は玉に若干の遊びが生じるよう形成されている。そのため原理的には、玉と軌道輪は1点で接触している。しかし、無限に小さい点に荷重がかかると、そこには無限大の圧力が生じる。実際には、玉は軌道輪と接する際に若干変形し、ちょうどタイヤが地面に接したときのように少し偏平になる。玉が接した軌道輪の表面もわずかにへこむ。したがって玉と軌道輪の接点は有限の大きさとなり、圧力も有限となる。また、玉は部分的に異なる速度で回転しているため、変形した玉と軌道輪は完全に滑らかに転がるわけではない。つまり、玉と軌道輪の接点には滑ろうとする力と転がろうとする反対の力が同時にかかっている。このため全体として軸受は引きずりながら回転する。
転がり軸受の多くは、転動体同士がぶつからないよう保持器(ケージ)を使っている。それによって転動体同士が擦れ合うことを避け、詰まることを防ぎ、結果として磨耗と摩擦を低減させる。保持器を使った転がり軸受は、17世紀中ごろジョン・ハリソンが時計を製作する過程で発明した[1]。
種類
[編集]転がり軸受には様々な種類があり、それぞれ特定の荷重に特化しており、長所と短所がある。以下に例を示す。
玉軸受
[編集]
玉軸受は転動体として円柱ではなく玉を使う。玉軸受はラジアル荷重(軸に対して直角方向の荷重)とアキシャル荷重(軸に平行な荷重)の両方を支持できる。荷重が軽ければ、玉軸受はころ軸受よりも摩擦が小さい。玉軸受は内と外の軌道輪がずれていても機能する。
ころ軸受
[編集]
ころ軸受 (roller bearing) は、転動体として直径より長さの方が若干大きい円柱を使う。ころ軸受は玉軸受よりもラジアル荷重の許容量が大きいが、アキシャル荷重の許容量は小さく、アキシャル荷重がかかると摩擦が大きくなる。軌道輪の内輪と外輪がずれると、玉軸受より急激に荷重許容量が低下する。
ころ軸受は、転がり軸受の中でも最初に考案されており、その起源は紀元前40年以前に遡る。
針状ころ軸受
[編集]
針状ころ軸受 (needle roller bearing) は非常に細長い円柱を転動体として使う。転動体が細いため、軸受の外径は内径より若干大きいだけで、他の軸受けよりも薄い。しかし転動体の直径が小さいと軌道輪と接した部分が鋭く曲がるため、軸受の疲労は比較的早い[要出典]。
円すいころ軸受
[編集]
円すいころ軸受 (tapered roller bearing) は、円すい台形の軌道輪と円すい台形の転動体を使う。ころ軸受はラジアル荷重しか支持できないが、円すいころ軸受けはラジアル荷重もアキシャル荷重も支持でき、接触面が大きいために玉軸受より荷重許容量が大きい。円すいころ軸受は例えば、自動車(トラックやバスを含む)の車輪の軸受に使われている。欠点は製造工程が複雑な点で、玉軸受よりもコストがかかることが多い。また、大きな荷重がかかると円すいがくさびのように作用し、転動体を軌道輪から押し出すように力がかかる。すると軌道輪の襟部分と接触して摩擦が増大する。
球面ころ軸受
[編集]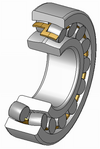
球面ころ軸受 (spherical roller bearing) は、中心が太く両端が細い転動体を使い、それに合うような形状の軌道輪を使う。球面ころ軸受は斜め方向の荷重であっても自動的に調整して支持できる。しかし製造が難しく高価で、球面ころの各部は異なる速度で回転しようとするため軌道輪との接触面に逆向きの力も働き、玉軸受に比べて摩擦が大きくなるという欠点がある。
スラスト軸受
[編集]
スラスト軸受は、垂直な軸などのアキシャル荷重を支持するのに使われる。玉、円すい、円柱などの転動体が使われる。転がり軸受以外の軸受も使われている。
用途
[編集]航空宇宙
[編集]航空宇宙用軸受は航空機などに使われる軸受で、高い精度を要求される。高精度の小型玉軸受が燃料制御システム、商用航空機、軍用誘導システムなどの航空宇宙システムで使われている。
車軸
[編集]回転摩擦が低いことから、車軸の軸受としてよく使われている。
その他
[編集]転がり軸受の多くは回転荷重や振動荷重を支持する設計だが、直線運動用の設計も存在する。典型例としては、引き出しを支持する構造がある。また、軸方向に動く軸を支持する軸受もある。そのような軸方向の動きを支持する軸受をリニア軸受 (linear motion bearing) と呼び、丸太で岩を運ぶのと同じような動作をする。ラック・アンド・ピニオン装置が自動車のステアリング機構に広く採用される以前は、リニア軸受が使われていた。
故障・破損
[編集]転がり軸受は理想的ではない条件でよく使われているが、ちょっとした問題が原因で突然破損することがある。例えば、平坦で真っ直ぐな道路上で、ちょっとした振動で軌道輪と転動体の間から潤滑剤が漏れ出すことがある。潤滑が不足すると軸受は回転していなくても故障しやすくなる。
軸受には寿命と荷重許容量を制限する3つの問題として、摩滅、疲労、圧力による融合がある。摩滅は、硬い汚染物が軸受に入り込んで材料を削っていく現象である。疲労は、荷重がかかったり解放されたりを繰り返すことで材料が破損する現象である。転動体が軌道輪に接触したとき、常に何らかの変形が生じるため、疲労の危険性がある。転動体が小さいほど変形が激しいため、疲労も早まる傾向がある。圧力による融合は、2つの金属部品に高い圧力がかかることで一体化してしまう現象である。転動体や軌道輪は滑らかに見えるが、顕微鏡レベルで見れば凹凸がある。そのため、微細な点に強い圧力がかかって、そこから潤滑剤が排除されることがある。このため顕微鏡レベルで転動体の一部が軌道輪に融合することがある。軸受は回転し続けるため、通常は融合が壊れるが、軌道輪と転動体がくっついたままになることがある。
軸受の故障や破損には様々な原因があるが、その多くはこの3種類に帰結する。例えば、潤滑不足の軸受が故障するのは潤滑剤が足りないことが直接原因ではなく、それによって疲労と融合が発生し、さらにそれによって微細な金属片が生じて磨耗するのが原因である。フレッティング磨耗も同様の現象である。高速回転では、潤滑油の対流によって軸受の金属の温度が低下する。潤滑油は軸受で生じた摩擦損失のためのヒートシンクになる。
制約とトレードオフ
[編集]
軸受の各部品には様々な設計上の制約がある。例えば、軌道輪は複雑な形状となっていることが多く、製造が難しい。転動体は、形状は単純だが小さい。転動体は軌道輪上で激しく変形するため、疲労が蓄積しやすい。軸受にかかる荷重はその回転速度にも影響される。転がり軸受は100,000rpm以上の速度で回転することもあり、その場合の荷重は単なる重量ではなく運動量の影響の方が大きい。転動体が小さければ、それ自体が軽いので運動量も小さいが、軌道輪と接したときの変形の度合いも激しいため、疲労による損傷が発生しやすい。転がり軸受の最大回転速度は 'DN' で示されることが多く、これは直径(mm)と最大回転数(rpm)の積である。アンギュラ玉軸受のDNは210万以上にもなるものがあり、高速回転と高精度を要求されるロケットなどの用途にも使われている[2]。
材料の選択も重要である。硬い素材は磨耗には強いが、疲労による損傷が発生しやすい傾向がある。そのため用途によって最適な材料を選択することが重要である。転がり軸受の材料としては鋼がよく使われるが、プラスチック、ガラス、セラミックスなどもよく使われている。材質の小欠陥(不規則性)は軸受の故障の大きな原因の1つである。19世紀後半の軸受の最大の改良は均質な材料を使うようになった点であり、新素材や潤滑よりも大きな改善となった。潤滑剤の特性は温度や荷重によって変化するため、用途によって最適な潤滑剤は異なる。
軸受は使用していると磨耗していくが、設計者は軸受の大きさとコストを寿命と天秤にかけて設計する。軸受を低温で清潔に保ち、推奨荷重以内で使えば、顕微鏡レベルの素材の欠陥がなければ、極めて長寿命に動作し続ける。したがって、冷却と潤滑と密封が軸受の設計の重要な部分を占めている。
必要とされる寿命も用途によって異なる。例えば、Tedric A. Harris は Rolling Bearing Analysis[3] の中で、スペースシャトルの酸素ポンプについて、ポンプが汲み上げる液体酸素と軸受の潤滑油を適正に分離できず、酸素と化学反応して発火するなどの故障が頻繁に起きたと記している。これを解決するため、軸受の潤滑剤として酸素を使ったという。液体酸素は潤滑剤としては性能が悪いが、そのポンプが動作するのは数時間だけなので、それでも十分だった。
動作環境や保守しやすさも設計上の重要な点である。軸受には、定期的に潤滑剤を加える必要があるものもあるが、工場でシールで密封して寿命が尽きるまで保守不要な軸受もある。潤滑剤に不純物があると磨耗が起き、軸受部品の寿命を短縮することになる。また、潤滑剤に水が混じっていると故障の原因になることが多い。
関連項目
[編集]脚注・出典
[編集]- ^ Sobel, Dava (1995). Longitude. London: Fourth Estate. pp. 103. ISBN 0-00-721446-4. "A novel antifriction device that Harrison developed for H-3 survives to the present day - ...caged ball bearings."
- ^ Design of liquid propellant rocket engines -Dieter K. Huzel and David H.Huang pg.209
- ^ Harris, Tedric A. (2000, 4th edition). Rolling Bearing Analysis. Wiley-Interscience. ISBN 0-471-35457-0
参考文献
[編集]- Johannes Brändlein, Paul Eschmann, Ludwig Hasbargen, Karl Weigand (1999, 3rd edition). Ball and Roller Bearings: Theory, Design and Application. Wiley. ISBN 0-471-98452-3
外部リンク
[編集]- 転がり軸受の潤滑について(英語) (PDF) Schaeffler
- NASA technical handbook Rolling-Element Bearing (NASA-RP-1105)
- NASA technical handbook Lubrication of Machine Elements (NASA-RP-1126)
- How rolling-element bearings work
- Kinematic Models for Design Digital Library (KMODDL) - コーネル大学の機械についての動画や画像のサイト。 機械工学関連の古典的書籍の e-book library もある。